Sorry… This site requires a JavaScript enabled browser.
Splurging £50,000 on an ex-demo wholecrop header might have put an end to time-consuming breakdowns, but it’s been a difficult expense for Graham Hayllar to justify.
For the past few years, he and his team had been muddling on with an increasingly troublesome 13-year-old Disco 520, but they could ill afford the downtime at such a busy time of year.
“It’s a lot of money for a machine that only does a month or so’s work, but it’s an important service for our customers and one that hopefully keeps us in with them for the grass silage.”
He briefly toyed with the idea of making one in the workshop but, with time limited, the only sensible option was to buy another.
The ex-demo 500P model from Rickerby offered a decent saving over buying new, and the fact he got £20,000 for the old one helped soften the blow.
“I still can’t get my head around the price, but it has gone well and the larger auger helps draw the crop in better. If we can get a good 10 years out of it, it might start to look less expensive.”
See also: NAAC contractor price guide 2023-24
Graham Hayllar © James Andrews
Another update to the grass kit armoury is a new Claas Liner 2900 rake, which came in at £25,500, up £5,500 from the last 2900 that was purchased three years ago.
The design has seen little change, so this significant price rise is purely down to inflation. Even the troublesome Y-gearboxes and crown wheels and pinions haven’t been upgraded.
Claas Liner 2900 rake © James Andrews
“Rakes just aren’t built to last and, year after year, manufacturers fail to address the main problems – I’ve found Claas models to be some of the most reliable, but it’s the best of a bad bunch, really.”
For this reason, he runs two rakes on a three-year replacement policy.
The hope is that this avoids breakdowns, but he has still been caught out by failed crown wheels and pinions, which cost about £800 each in parts alone to repair.
With the Jaguar 950s able to cope with such large volumes of grass, Graham is also questioning whether a four-rotor rake is required.
However, as this would only be required for light later cuts – early crops are pretty heavy in Cumbria – and has more than twice the number of moving parts to go wrong, it’s another hard one to justify.
It hasn’t all been about grass kit updates, with a 2012 Bargam Grimpeur self-propelled sprayer recently joining the fleet.
This arrived after a brief stint with a 4,000-litre, 24m Chafer trailed machine that was brought in to run alongside the trusty 3,600-litre Case.
It looked smart, but it proved hard to handle on slopes and the boom levelling was a little erratic.
Bargam sprayer © James Andrews
While he was struggling to get to grips with it, Graham spotted the Bargam for sale and liked the look of the hydrostatic transmission driving mechanical axles.
Added to that, it had a decent spec with auto-section control, air shut-off, boom recirculation and a system that allows the boom to be washed out separately to the tank – handy if a job gets rained off partway through.
A chat with a friend who owns the same model sealed the deal and he bought it for £30,000 on 5,000 hours. As the Chafer was sold on for the same £18,000 he paid for it, the upgrade cost was tolerable.
Before being pressed into service, the Grimpeur was kitted out to run Greenstar guidance with an Autotrac Universal steering wheel and cabling that allows it to share a dome and screen with the 6430.
It’s gone well and has helped take the pressure off the tractor fleet, particularly as the 6195R is laid up with transmission troubles (see “Workshop: Stuffed turbos and a major gearbox rebuild”).
The only thing that’s taken some getting used to is the complicated joystick with eight buttons that can each perform three different functions.
“To start with I was travelling down the field doing all sorts of weird things like folding the boom while attempting to level it, but I’m gradually getting used to it.”
Last winter’s workshop project to build a remote-controlled umbilical slurry pumping trailer has proved a prudent move, as heavy rainfall has made ground too wet to carry tankers.
It and the other manual pumping trailer have been working overtime as a result, supported by the home-made nurse tank on more remote blocks of land.
The remote-controlled unit has gone well and has already pumped about 30,000cu m of slurry this season. It’s only had one significant problem – a glitch with the remote turn-off function – which should soon be sorted.
After years of trying find a simple way of organising, recording and invoicing jobs, Graham has signed up for a trial of AgDrive’s management software.
The system allows drivers to record jobs on their phone as they are being carried out, and once they press a button to say that it has been completed, the information is automatically uploaded.
They can even say whether they’ve used their own or the customer’s fuel.
So far, it looks like a significant step up from the previous process of adding notes to a WhatsApp group which, in turn, replaced notebooks in the tractor cab.
“The notebooks aways seemed to get damaged or lost, and although the WhatsApp group worked, I still had to manually sort through the messages,” says Graham.
“I like the fact that the system puts all the jobs in one place and assigns them to the correct customer, so all I need to do is check them over and approve them for invoicing.”
Another benefit is that it records customer details and maps field locations and their sizes, so operators can find where they are going, know the size of the area they’ve got to work, and they can easily make contact if they have any questions.
Graham also hopes it can be used for maintenance records, which are currently jotted on a whiteboard in the workshop.
“It costs £10 a month for the system and £5 per operator, so I’d be looking at paying about £400/year – on first impressions I think it’ll be worth it.”
After noting in our last report that Graham’s fleet of high-hour, remapped tractors has given very little trouble, we’ve jinxed it, and things have started to go awry.
Turbos on both the 6430 and 6150R have recently packed up, with the former getting a simpler fixed-vane replacement rather than an original variable-geometry unit from John Deere.
This also involved sending the ECU to Derbyshire-based tuner The Derv Doctor, which has pushed power output up to a giddy 175hp.
The 6150R received a genuine remanufactured turbo purchased from Cornthwaites at a cost about £2,500, and this has also been remapped to 219hp.
But the biggest calamity was when one of the universal joints on the driveshaft between the engine and gearbox on the 6195R snapped, damaging the end of the main shaft in the Autopowr transmission in the process.
© James Andrews
It happened while hauling silage, shortly after it was recorded running at 235hp at the local Winders Dyno Day charity event.
“We know those shafts can give trouble, so we regularly inspect them for signs of wear and replace them if they look dodgy,” says Graham.
“This one let go without much warning though, and I don’t think we can blame the stint on the dyno.”
Initially, he and mechanic Chris Hunter fitted a new driveshaft and it went fine. However, the damage to the end of the gearbox shaft meant the transmission couldn’t hold oil.
© James Andrews
So they had to take the gearbox out and strip it down – a job that requires complete cab removal – before rebuilding it with a new £3,000 shaft sourced from Nick Young Tractor Parts.
In total, the bill is expected to run to about £5,000, which although a considerable hit, is a fraction of the price of a remanufactured Autopowr transmission which they found listed by John Deere at £25,000.
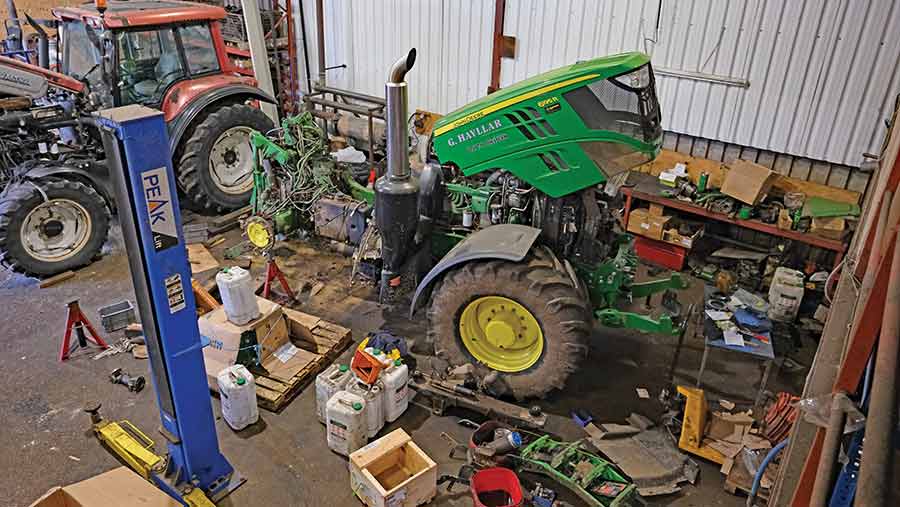
© James Andrews
© James Andrews
Using contractors saves you time and money. Now you can book, track and pay all in one place. Register for early access today.
Ask us a question
Visit our Know How centre for practical farming advice