Sorry… This site requires a JavaScript enabled browser.
Last year’s sub-par maize yields have forced anaerobic digester (AD) plants to expand their acreages to shore up dwindling feedstock supplies, and that has meant more work for P Russon & Sons.
The business is on course to match its 2020 harvesting record of 4,000ha, and the anticipated workload will inevitably expose any weaknesses in the machinery fleet.
With a big autumn looming, servicing, maintenance and repairs have been top of Tim Russon’s agenda, and ensuring the four foragers are race-tuned has been the priority.
See also: Perfect storm of price rises causing carnage for Devon contractors
Tim Russon © MAG/Oliver Mark
The headline acts are a pair of one-year-old Claas Jaguar 970s, which are each expected to chop 60ha/day.
For maize, these are supported by a third machine that should contribute another 40ha to the daily target, with a fourth on standby in the shed should anything go wrong.
Claas Jaguar 850 © MAG/Oliver Mark
However, the current third machine, a 15-plate 870, is causing headaches.
Having already suffered a sheared half-shaft while cutting miscanthus earlier this year, a subsequent mid-season service revealed metal filings in the gearbox oil.
Further investigation showed there to be a handful of missing gear teeth.
The strip-down and repair process is now well under way, but questions over the ailing 870’s reliability have encouraged a rethink.
“The 870 has been to the moon and back chopping maize and miscanthus and it’s just about worn out. I’m uncomfortable about relying on it for a big maize season so, once fixed, it’ll be relegated to fourth,” says Tim.
JCB 4220: Next up for replacement © MAG/Oliver Mark
That means it will be solely charged with cutting a good chunk of the 1,600ha of miscanthus, unless it is called upon in the autumn to fill in for an unexpected breakdown.
To accommodate the rejig, the firm’s current backup machine, a 2007-built Jaguar 850, will be rehomed – but only once its custom-built miscanthus drum has been removed and a conventional chopping cylinder fitted in its place.
Its successor will be a high-spec, two-year-old Jag 880.
“I considered buying a new model but, at £307,000, it would cost £100,000 more than the second-hand machine for the sake of 1,500 hours. That works out at about £66/hour, so it doesn’t really stack up.
“Plus, I don’t want a new machine on miscanthus. As well as the wear and tear, there’s a significant fire risk, and I’d prefer a lower value insurance claim.”
Though the foragers take a fair bit of punishment cutting miscanthus, Tim’s prices are broadly on a par with maize harvesting.
The tyres get plenty of abuse, with the tough stems pitting the rubber until it becomes porous, and the metal in the header wears quickly.
But these added costs are offset by the fact that fuel consumption is lower and there’s no damage to the blades, crop accelerator or discharge chute, as the material is dropped straight from the cylinder to the ground.
The steady churn of tractors has continued this year with the arrival of a fourth JCB Fastrac 4220 to replace one of the five ageing 2170s.
“The lads like the Fastracs and they’re my preferred choice. They’re good for road work and we’ve found them pretty reliable, provided they get regular maintenance and servicing,” says Tim.
“They also tend to depreciate slowly, which means I can push the hours higher without affecting resale value.”
The recently departed 2170 is a prime example, having arrived on 3,500 hours for £40,000 and left 6,000 hours later for the same fee.
“I felt I’d had the best of it and, though there’s always the temptation to hang on for longer, the chances of getting my fingers burned rapidly increases.
“In the end, it cost me a set of BKT tyres, at about £4,000, plus a bearing in the rear axle, a set of brake shoes and a steering pipe – all of which we can do ourselves.”
Its replacement is a near-new 4220 on 300 hours. As with previous Fastrac replacements, Tim was keen to avoid having to shell out for the newer iCon model, which commands a price premium of up to £20,000.
“At some point I will have to take my medicine and buy an iCon. But I’ll resist for as long as I can, as it’s expensive, I’ll get no more work out of it compared with an older model, and it has far more technology than I need for hauling silage.”
Next on the chopping block is an 18-plate 4220 that has now clocked 7,500 hours and which, provided there are no hiccups, should make it to 9,000 hours by the end of the maize season.
“Between 9,000 and 10,000 hours tends to be my tipping point for Fastracs. Beyond that, they become a bit more of a gamble – they’re harder to sell, residual value starts to take more of a hit and I’m potentially letting myself in for a big, costly repair.
“I wouldn’t take the New Hollands to those sorts of hours though. From my experience, the clutch packs and cab mounts wear, and I get a bit nervous about the brakes – particularly if they’re thrashing up the road with a silage trailer on the back.
Currently inhabiting the workshop is a cab-less 6,500-hour Fastrac 2170 suffering from a sheared gearbox shaft.
With the bill for a new shaft and replacements for the mashed cogs coming to £6,500, Tim instead opted for a complete second-hand unit.
It cost a modest £2,200 from Vickery Plant in Leicestershire.
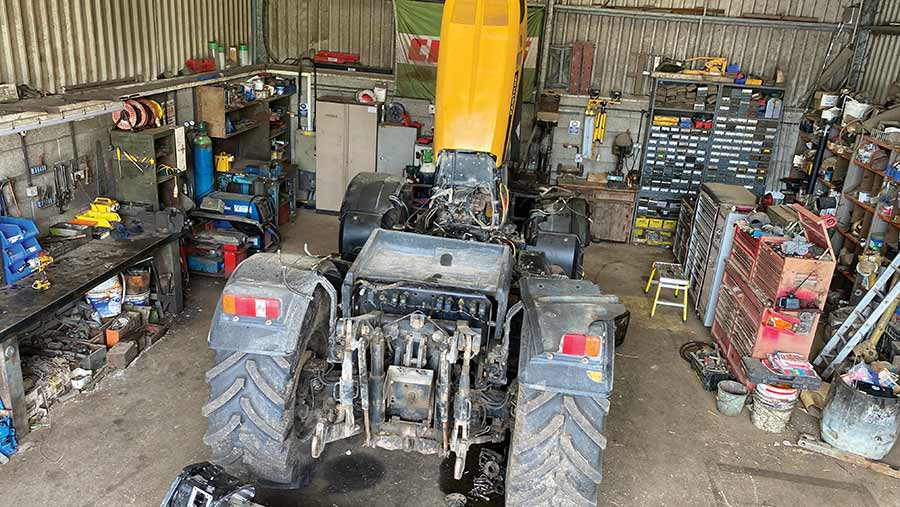
© MAG/Oliver Mark
© MAG/Oliver Mark
The trailer fleet has also been subject to a big investment.
While the five replacement Baileys were budgeted for, concerns over the legality of unsheeted silage loads forced an unforeseen £60,000 splurge on 18 Transcover Easy Sheets.
“There’s been a lot of press coverage about the police and Vosa [Vehicle and Operator Services Agency] toughening their stance on insecure trailer loads,” says Tim.
Bailey trailers © MAG/Oliver Mark
“I can’t afford to have drivers getting points or fines for illegal transportation, nor do I want my trailers impounded.
“It’s obviously a lot of money, which makes it tough to swallow, but it was actually an easy decision. As a professional contractor working for blue chip companies, I have to play by the rule book.”
Once fitted, every load of silage will be sheeted from the field, eliminating the risk of crop blowing out and blocking gullies and drains.
The maize drilling area was up about 30% on last year, with low cereal prices making it easier for AD plants to convince farmers to make the switch from late-season barley.
As a result, Tim took a last-minute decision to replace one of his three trailed Kverneland eight-row Optimas with a mounted Amazone Precea 6000-2CC of the same size.
The eight-year-old model was moved on for £20,000, representing a modest £2,500/year depreciation.
That was thanks, in part, to a new set of discs and a full service that ensured it was sold in ready-to-work condition.
Amazone Precea 6000 © MAG/Oliver Mark
“I’ve always run KVs as they tend to be good value for money, but Amazone was able to supply me a drill immediately and I’ve been impressed by the build quality – to such a degree that I’ll probably look to have another in the future.”
Adding a mounted model to the otherwise trailed fleet has also provided more flexibility, particularly during the wet spring.
“It can keep pace with the KVs and, without the trailed wheels, there’s far less mess and compaction on delicate headlands.
“It’s handier for small, odd-shaped fields and it also travels on the road far better – with the trailed machines we’re limited to 25kph, but when it’s mounted on the Fastrac we can do 60kph.
“The limiting factor tends to be farmers’ ability to prepare ground ahead of the drills, as we’ve got the capacity to cover 200ha/day in the right conditions.”
The final change is on the muckspreader front, with a Bunning Lowlander 150 HBD arriving in June to replace an eight-year-old horizontal beater version from the same brand.
The business now runs two HBDs to handle the rising demand for spinning-disc models that can accurately apply well-rotted muck, chicken litter and digestate to 24m.
Bunning Lowlander 150 Mk5 HBD © MAG/Oliver Mark
The new version brings the added benefit of a rear body section and rotors that are roughly 200mm wider than before.
“I wanted more capacity, which the wider backend will provide, and the ability to accurately spread strawy muck that, with the vertical beaters, we can only throw to 6-8m.
“The upgrade cost £35,000, for which I’ve got a machine that is eight years newer and far superior. Plus, the extra technology, including weigh cells, means I can print a ticket to show exactly how much has been spread, and where.”
Using contractors saves you time and money. Now you can book, track and pay all in one place. Register for early access today.
Ask us a question
Visit our Know How centre for practical farming advice