Powered by
Latest Articles in “Markets”
Monthly Report – June
Short Term Commodity Outlook: Aluminum & Zinc
Electromobility
KS HUAYU Expands its Electromobility Portfolio: New Order from Premium Automaker for Battery Carriers
Business Collaboration
GF and Bocar Group to Enter into a Global Collaboration
Monthly Report – May
Short Term Commodity Outlook: Aluminum & Zinc
Latest Articles in “Technologies”
Electromobility
SJM Presents Itself for the First Time in Europe at EUROGUSS
Sustainability
Light Metal Foundry at the BMW Group Plant in Landshut Relies on Innovative Multi-Plate Mold Technology for Chassis Casting Parts
Quality Assurance
Yxlon Sets a New Benchmark in Computed Tomography
Release Agents
Greater Efficiency and Sustainability with the Right Release Agent
Latest Articles in “Industries”
High Pressure Die Casting
Customised Performance as Standard: ItalPresseGauss Evolves Die Casting with Launch of Lean Modular Design
Friction Stir Welding
Lightweight Construction for the Automotive Industry with Friction Stir Welding
Electricity Instead of Gas
Light Metal Foundry at BMW Group’s Landshut Plant Relies on Electric Heating Stations for Aluminum Smelter
Megacasting
Handtmann Invests in Megacasting
Latest Articles in “Events”
Product News
The MAXImolding® Process, the MAXImolding® Machine, Multi-Injectors-Press in Smart Digital Foundries
EUROGUSS 2022 Program
Self-Initiative, Circular Economy and Carbon Footprint – This Is How Sustainable the Die Casting Industry Is
Product News
KS HUAYU AluTech Showcases Top Casting Expertise at EUROGUSS 2022
Related Vendors
The MAXImolding! Technology GmbH will present “The Future of Lightweight Metal Parts: The MAXImolding® Process, the MAXImolding® Machine, Multi-Injectors-Press (TERApress™ at small size) in Smart Digital Foundries” at the EUROGUSS trade fair on the 8th, 9th and 10th of June at 1:30 pm local time at their booth 9-458/j.
Semisolid metal injection molding is a molding process that involves filling a mold with the metal in a partially molten state in which globules of solid are homogeneously dispersed in the liquid. The four currently used semisolid metal casting processes, Thixomolding®, Thixocasting®, Rheocasting®, and stress induced melt activation (SIMA), are complex to start and very highly maintenance intensive. The processes, cold or hot chamber die casting or vacuum die casting, do not fulfill end user expectations for quality, simplicity, energy savings, safety, economy, and environmental responsibility. This is where the MAXImolding® process comes in and further simplifies and improves the Thixomolding® process. MAXImolding® process involves mechanically stressed chips or chips in preferred metallurgical configurations. The selected chips are fed into a pre-conditioning unit called scrubber. The chips are heated with a precise temperature control under atmosphere of Argon in our vertical injection molding machine. We call this process solid-to-solid molding because we start with solid chips, produce semisolid slurry, and end with solid net-shape parts out of the mold. The process is fully enclosed in the MAXImolding® machine. We use a very small amount of Argon to prevent chips oxidation.
Dr. Frank Czerwinski has been working for decades in the research fields of “Semisolid Metallurgy” and improvements of Magnesium Injection Molding Machines. He wrote that the thixotropic slurry containing spherical solid particles in the melt could be obtained in the thermal mass reactor under the sole influence of heat. Figure 1 shows the process and the microstructure of the alloy. The adopted process does not require screw rotation. It is not necessary to shear the chips to produce semisolid slurry that contains spherical solid particles in the melt. Precise temperature control of chips fed under gravitation from the top to the bottom of the reactor is only what is required. Elimination of screw for shearing is a major simplification of the process. The generation of thixotropic slurry that contains spherical solid particles in the melt can be done in the thermal mass reactor under the sole influence of heat.

Precise temperature control of chips fed under gravitation from the top to the bottom of the reactor is only what is required.
The core of the idea starts with the question: How can we build a hybrid machine that can produce high-integrated parts that are nearly defect-free with little energy and material, very quickly, and without environmentally harmful gas emissions? A machine that combines the advantages of Thixomolding® and Hot and Cold Chamber high-pressure die casting machines (HPDC) and avoid their disadvantages? The answer to this is offered by semisolid (semi-liquid) metal injection molding. A molding process in which a mold is filled with the metal in a partially molten state.
The advantages of this procedure are as follows:
The MAXImolding® machine is the result of an advanced development of the magnesium injection molding machine. Advancing Thixomolding® technology by eliminating the extruder with a screw as a major disadvantage of Thixomolding®, resulted in MAXImolding® vertical oriented machine.
This process offers many improvements compared to the environmentally unfriendly, high-energy consumption hot and cold chamber high-pressure die castings (HPDC) machines. As we understand, most products made from magnesium today are being made by die casting. The magnesium casting was left behind in the technology curve. However new semisolid metal injection molding machines offer much improved processing capability. For example, the new machine does not require a melting pot of overheated molten magnesium during casting that requires the SF₆, SO₂, or R134a cover gas (greenhouse gas pollutant) and does not need the energy to maintain the molten metal in an overheated molten state. Rather, solid magnesium particulates can be used. The chips, with preferred metallurgy is used and fed into the magnesium main processor that (by adding heat) converts the solid magnesium into a semisolid slush of material, very similar to crashed ice at temperature just above 0 °C.
This semisolid structure operates at temperatures often 200°C below the current magnesium die casting processing temperatures resulting in significant energy advantages. This semisolid magnesium alloy is then injected into a permanent mold, very similar to plastic injection molding process. The MAXImolding® process is fully enclosed; solid-to-solid, part shaping process that can be operated in ordinary manufacturing plants.
By clicking on „Subscribe to Newsletter“ I agree to the processing and use of my data according to the consent form (please expand for details) and accept the Terms of Use. For more information, please see our Privacy Policy.
Declaration of consent
Naturally, we always handle your personal data responsibly. Any personal data we receive from you is processed in accordance with applicable data protection legislation. For detailed information please see our privacy policy.
I consent to NürnbergMesse GmbH, Exhibition Centre, 90471 Nuremberg, including any affiliated companies according to §§ 15 et seq. AktG (hereafter: NürnbergMesse) and Vogel Communication Group GmbH & Co. KG, Max-Planckstr. 7-9, 97082 Würzburg, including any affiliated companies according to §§ 15 et seq. AktG (hereafter: Vogel Communications Group) using my e-mail address to send editorial newsletters. I have accessed lists of the respective companies here for Vogel Communications Group
Newsletter content may include all products and services of any companies mentioned above, including for example specialist journals and books, events and fairs as well as event-related products and services, print and digital media offers and services such as additional (editorial) newsletters, raffles, lead campaigns, market research both online and offline, specialist webportals and e-learning offers. In case my personal telephone number has also been collected, it may be used for offers of aforementioned products, for services of the companies mentioned above, and market research purposes.
In case I access protected data on Internet portals of NürnbergMesse including any affiliated companies according to §§ 15 et seq. AktG or Vogel Communications Group including any affiliated companies according to §§ 15 et seq. AktG, I need to provide further data in order to register for the access of such content. In return for this free access to editorial content, my data may be used in accordance with this consent for the purposes stated here.
I understand that I can revoke my consent at will. My revocation does not change the lawfulness of data processing that was conducted based on my consent leading up to my revocation. To declare my revocation I must use this contact form. In case I no longer wish to receive certain newsletters I have subscribed to, I can also click on the unsubscribe link included at the end of a newsletter. Further information regarding my right of revocation and the implementation of it as well as the consequences of my revocation can be found in the privacy policy, section editorial newsletter.
The simplicity of the process makes it easy to operate in any region of the world without the need for extensive training. The MAXImolding® vertical orientation saves floor space and improves material flow. Fully automated part removal is easily integrated by simple robotic devices. Magnesium solidification in the mold releases captured heat of fusion via an innovative heating/cooling process for re-use.
MAXImolding® recycles this heat of fusion, by pre-heating the input magnesium chips. The energy savings alone allow the costs of parts to be competitive in the market compared to any other magnesium process known today. Carbon credits generated by this technology could be suitably marketed and sold as carbon shares on the open market to those who need to operate plants with high CO₂ output. To be able to improve on energy, reduce maintenance and improve on output quality, we replaced the barrel and screw with a new high thermal mass reactor in form of a cylinder. Symmetrical cylindrical mass is much easier to control heat and maintain stable temperature of the semisolid melt. The processing cylinder contains eight smaller processing cavities for AZ91D chips entering from the top, four on each left and right side and a larger bore in the middle of cylinder for injection piston. Heaters are placed around the cylinder and nuzzle from the top to bottom for uniform and precise heating. Lower platen with mold opens downwards creating safe part pickup access. When the mold is closed, the parting line of the mold is completely behind solid guards, making this process much safer when compared to the horizontal clamping machine. The removal of parts is simply done by any side entry device. Replacing the extruder with a high thermal mass reactor led to a precise temperature control and thus a more efficient and less maintenance intensive process is accomplished. Figure 2 below shows the schematic of the MAXImolding® machine.
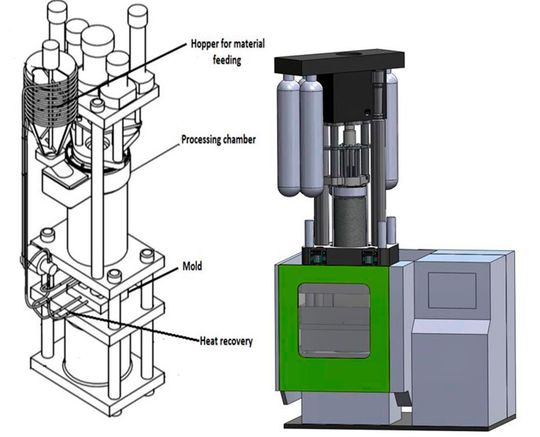
Let us start with the source material, and preparation in the MAXImolding® machine. Metal shavings, the magnesium particles in sizes 2×5 mm, also called chips, feed to a hopper with a chip levitation scrubber preprocessor flooded with argon or any other suitable cleaning medium. The Mg chips heat up to 200 °C with a precise temperature control. The oxidation is prevented by flooding with argon. The chips are then continuously dosed into the vertical injection molding machine and slowly heated from top to bottom in eight cavities heated by special resistive coaxial heaters. The heat returned from the mold is used to preheat the starting material (chips). The Mg chips coming from the preprocessor are preheated to approx. 200 °C. Further heating happens with argon in the thermal reactor in the form of a revolver. Several heating zones attaches to the outside wall of the cylinder. The semisolid slurry collects in a lower chamber. This viscous mass is then precisely metered under the centrally position injection piston.
The high melt pressure of 1000 bar and high speed up to 10 m/s is used to inject the slurry into a mold. The whole process requires a unified, vertical path of only 1.5 m, which means that the whole foundry line is shrinking to 4.5 m only. This makes the process more manageable. Alternative feedstock could be the specially formulated chips with preferred alloys configuration, then re-heated to desired forming temperature and injected into the mold while in the semisolid state. The semisolid metal mixture (slurry) is produced on demand and injected directly into the mold. The heated magnesium pathways and nozzle shutoff greatly reduces the total cycle time and improve part quality while keeping energy consumption low. Similarly, the processing of aluminum alloys is possible in a same way.
In 2021, Elon Musk from Tesla said, “With our giant casting machines, we are literally trying to make full-size cars in the same way that toy cars are made”. In 2020 IDRA Italy delivered the first OL 5500 CS (5500 ton-force) Giga press (giant house-sized “DCM”‒Die casting Machine) for the Tesla factory (machine #1) in Fremont, California. The single-piece casting for Model 3 will replace around 70 stampings, extrusions, and castings. The total weight of this Giga press was 410 tons. Swiss Buhler follows with an even bigger Giga press with 9200 tons of clamping force. While making bigger and bigger machines to make cars like toys is possible, bigger is not necessarily better for the environment and energy efficiency!
In 2017, the author (AS) said, “It will be possible to cast large size light alloy parts to suit full-size cars production without usage of metal sheet, stamping, welding etc.” How? By usage of MAXImolding® TERApress™ at small size, by combining semisolid metal alloy molding machines instead of giant casting machines called Giga press. The large structural parts, limited in size by mold size only, comes out of large mold by placing the multi semisolid melt delivery injectors, vertically, above or around a very large mold.
Apart from the die casting machine itself, the complete Giga casting cell for fluidized melt production needs further equipment like: melting furnace, holding furnace, dosing system, vacuum system, single or twin spraying unit(s), part removal robot(s), x-ray machine, quenching system, trim press for removal of runners and vacuum channels, return material shredder, part handling robots and other equipment for secondary operations like deburring, straightening, machining, assembly, cleaning etc.
Instead of “less is more” we have here “more is much more, and the bigger, the better”. When is a large casting cell large enough? These machines for the injection of fluidized melt, designed according to the principles “the bigger, the better” are an environmentally unsustainable solution. A Giga press requires large castings and structural parts made from large steel pieces, machined on only few available CNC machines in the world in faraway locations, which have a big environmental footprint. You need to transport heavy parts to the final location, assemble it with special machinery, and finally, perhaps even build a factory around the Giga press.
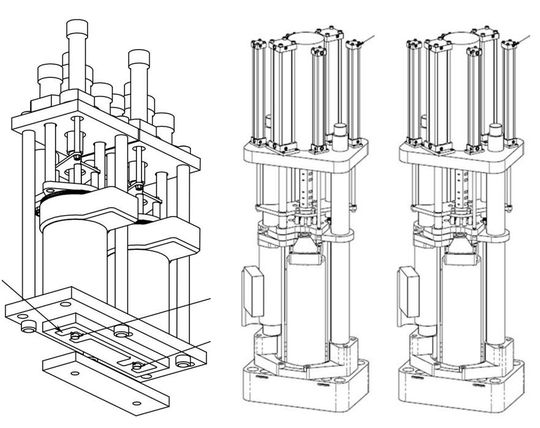
We suggest multiple, scalable, injector modules (see Fig. 3) for semisolid, non-fluidized melt, injecting simultaneously or sequentially to produce very large structural castings or very large surface, thin wall castings. This is a better approach to cast big parts. We envision placing multiple smaller injectors over a large surface of the mold and injecting a semisolid slurry to create castings of any large parts, like car side panels or rooftops. This way, it is possible to cast much better part with better part characteristics. That is why we are building multiple injectors for large surface parts made of magnesium or aluminum alloys.
The MAXImolding® process allows smaller, cost-effective factories, to produce any part for the car and staying competitive. Semisolid, non-fluidized melt originates from solid chips “on-demand” and the processing semisolid slurry is fully contained within the machine, which does not require separate generation and handling of the melt. We believe that the Giga press approach is prohibitively complex and environmentally unsustainable.
A novel “solid-to-solid” (from chips to parts) precise temperature control-based process incorporating the MAXImolding® semisolid metal molding machine with mold water mist cooling system and mold electrical heating system has been patented and is available for licensing and commercialization. Additionally, a patented manufacturing control system with data feedback coming from x-ray machine finally allows us to build a fully automated casting factory for 21st century. We hope that this will help us move in the direction of an advanced die casting process. A model of a fully automated die casting/metal molding process is depicted in Fig. 4 below. The operator is only required to power up the machine and ensure material is available and taken away. For example, the die casting wheel for a car would follow a basic sequence like this:
The operator would provide power to the semisolid casting/molding machine called MAXImolding®, follow an initial checklist related to supply of the material, initial parameters, and safety verification, and then press the „3D Wheel Type“ button on a touch screen, followed by the „Start“ button. The MAXImolding® machine would start casting/molding the first wheel according to proposed casting parameters by intelligent, cloud-based system (ML, AI, NN, SPC etc.) and, upon completion, the wheel would be outputted from the casting/molding machine and transported to the X-ray inspection system. The fully automated X-ray inspection system would determine the quality of the wheel. If the part is good, all information about this good wheel will be stored in a good wheel data set data base. The same process would be followed for the original production (process) data set, as well as the design 3D model data set. If the wheel is bad, information will be stored in a bad wheel data set data base.
Assuming that the wheel is bad, the knowledge system will determine which set of parameters need to be adjusted iteratively to improve wheel deficient characteristics, and a new set of inputs will be generated in the parameter generator. By way of a hypothetical example, the inspection may indicate that the wheel is not completely formed, indicating insufficient feedstock has been injected into the mold, commonly referred to as a short shot. The knowledge system determines a longer injection period is appropriate, and iteratively instructs the parameter generator to delay the closing of the nozzle and inject more material. The next machine cycle is executed, serialized, and passed on to the inspection system. More data from the inspection system generates more information and allows for faster convergence to a set of parameters that yields good quality wheels. This process for producing magnesium wheels by closing the loop with data from an inspection system and accelerating convergence with data sets from good wheels and bad wheels as well as 3D model of the original design will allow the production of high integrity wheels with minimal rejects.
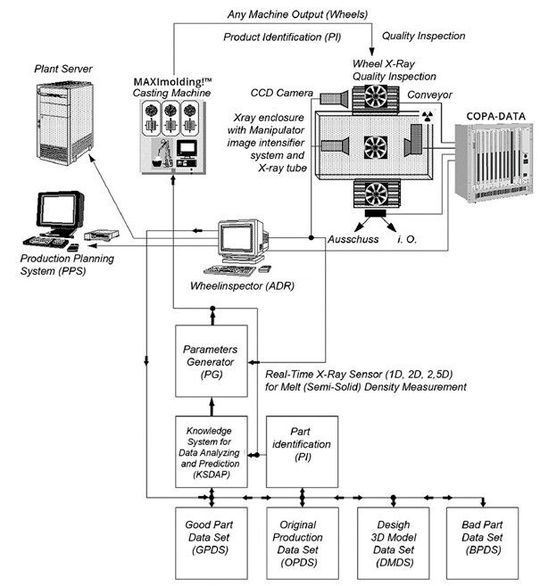
This is lean, an intrinsically safe, energy efficient, environmentally sound magnesium casting/molding foundry with no emission of gases outside of foundry parameters. All casting/molding machines and x-ray inspection machines, as well as proprietary linear robotics and machine vision systems integrated into this semisolid casting/molding process, will ensure the fast production of good parts, and maintain stable automatic closed loop process control.
Die Casting Event
The Excitement of the Die Casting Industry is Immense
This new solid-to-solid (S2S™) process, combined with an x-ray feedback control loop and applied mathematics (AI, NN,ML-machine learning, big data mining, etc.) as well as the use of self-contained fully operated modules based on the HyperComMachinery™ concept from Jacobsen Real-Time X-Ray Machinery Inc. Canada, it can revolutionize the classical die casting and injection metal molding industry. The semisolid magnesium metal alloy injection-molding machine can operate and create a fully automated casting/molding factory. It will ensure the fast production of good parts and maintain a stable automatic closed-loop process control. This is an intrinsically safe, energy and material efficient, environmentally sound magnesium-molding factory (aluminum foundry follows) with no emission of gases outside of factory parameters. All metal alloy molding machines and X-ray inspection machines, as well as proprietary linear robotics and machine vision systems integrated into this semisolid injection molding process, will ensure the fast production of good parts, and maintain stable automatic closed-loop process control wherever you are on this planet earth. The collection of process data for the same or similar parts worldwide (planetary molding) will be accessible via cloud and everybody can use it to start up and improve their processes of magnesium and aluminum metal alloy casting/molding.
Copyright © June, 2022 by MAXImolding! Technology GmbH
(ID:48407017)
Related content
Cookie-Manager Imprint Media General Terms & Conditions Privacy Help
Copyright © 2022 Vogel Communications Group
This portal is a brand of Vogel Communications Group. You will find our complete range of products and services on www.vogel.com
NürnbergMesse/Frank Boxler; gemeinfrei; MAXImolding! Technology GmbH; SP Süddeutsche Prüfanlagen GmbH; https://portal.handtmann.org/sites/Geschaeftsbereiche/Konzern/Holding/Marketing/Logo/Forms/Thumbnails.aspx?useFiltersInViewXml=1&FilterField1=FileType&FilterValue1=jpg&FilterType1=Computed&id=%2Fsites%2FGeschaeftsbereiche%2FKonzern%2FHolding%2FMarketing%2FLogo%2FLogo%20Englisch%2Ejpg&parent=%2Fsites%2FGeschaeftsbereiche%2FKonzern%2FHolding%2FMarketing%2FLogo; http://promove.ch/de/content/fondarex-sa; GF Casting Solutions AG; BMW Group; ItalPresseGauss S.p.A.; Grenzebach; Rheinmetall AG